Maintenance practices isn’t an expense; it’s an investment that saves you thousands in the long run.
Absorption chiller maintenance isn’t an expense; it’s an investment that saves thousands in the long run. A critical failure in your absorption chiller can lead to hours of downtime, costly repairs, and a spike in energy consumption. What could you have done to prevent it?
The answer is simple: chiller maintenance
Keep your systems running at top-level performance with our expert chiller maintenance contract services.
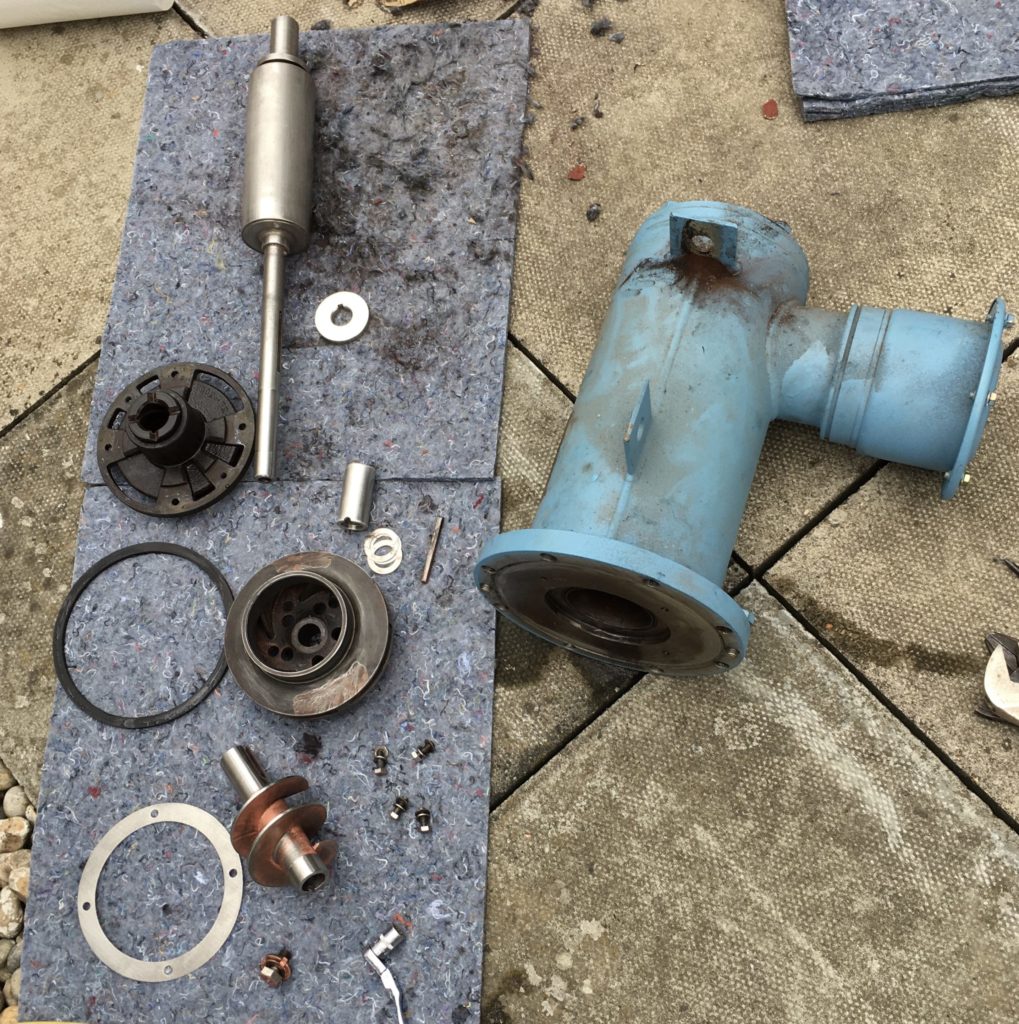
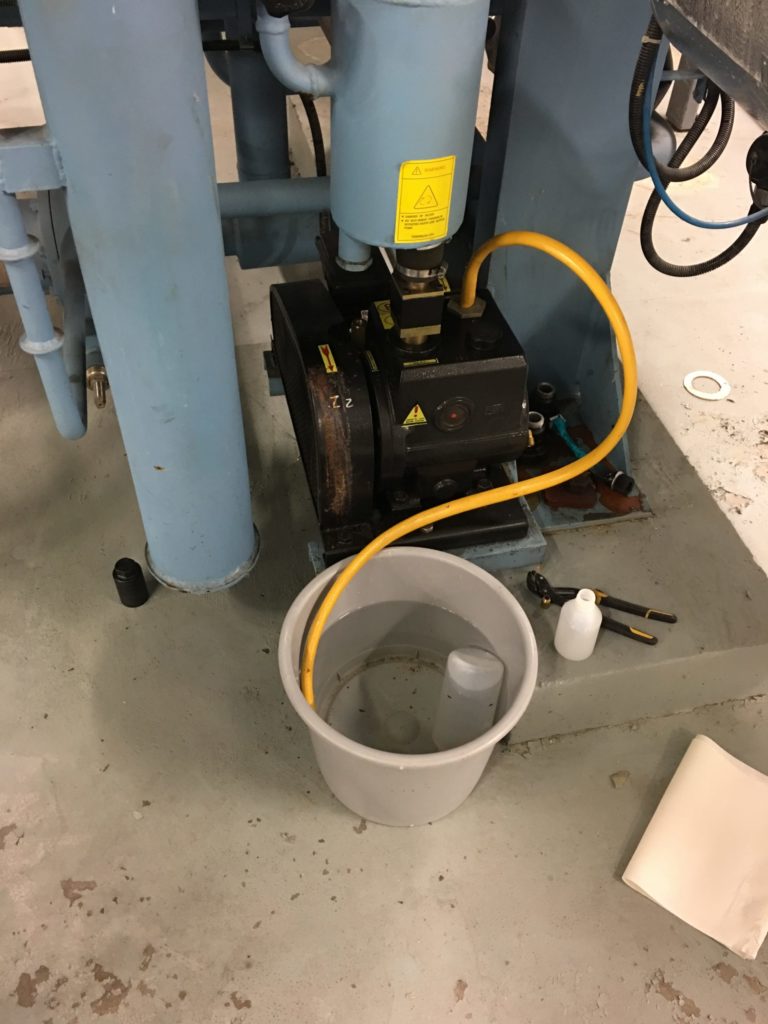
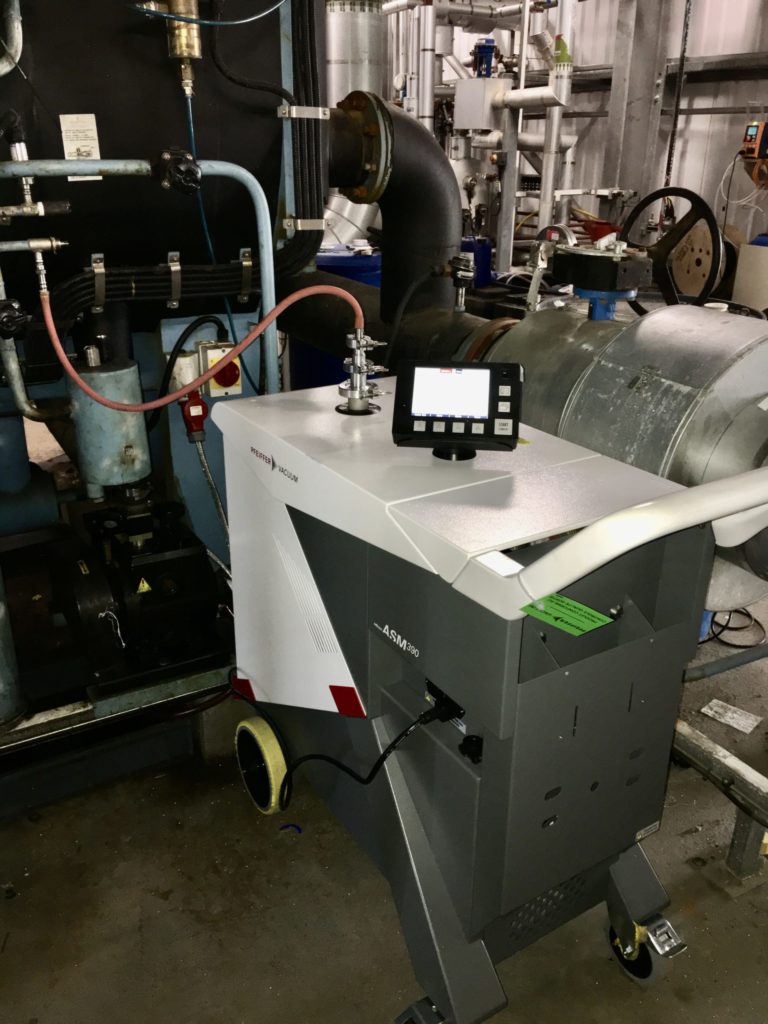
Vamtec’s guide to mastering absorption chiller maintenance: Keep your systems running at top-level
Optimize Absorption Chiller Efficiency : To maintain your chiller’s efficiency, neglect can lead to increased energy consumption for the same cooling output. This can result from fouling, leaks, or pressure imbalances. Regular maintenance of heat exchangers, purging systems, and solution pumps ensures the system uses less energy while delivering optimal cooling results. Our Thermax chiller maintenance and Carrier chiller maintenance services focus on maximizing efficiency for all major brands.
Extend lifespan and prevent system downtime: Preventive maintenance is key to reducing the risk of high-cost failures. Premature wear in solution pumps or vacuum pumps can lead to early failures and expensive repairs. By identifying early signs of wear in critical components, such as diaphragm valves, you can prevent unplanned issues. Vamtec provides robust absorption chiller service across the UK and Europe for all different type of absorption chillers, and absorption chiller leak repair to keep your systems operational.
Preventing System Fatigue: Improper maintenance increases system fatigue, leading to costly repairs that could have been avoided with simple weekly checks. Our chiller maintenance contract services are designed to detect risks early, ensuring your cooling infrastructure remains reliable. Whether it’s steam absorption chiller fix or routine inspections, we’ve got you covered.
Environmental sustainability: Absorption chillers are more environmentally friendly than compression chillers, utilizing waste heat or solar energy instead of electricity. Maintaining proper inhibitor levels in the lithium bromide (LiBr) solution and ensuring tight seals to prevent air leakage are critical to avoiding internal corrosion. Our LiBr chiller servicing includes lithium bromide analysis to ensure long-term efficiency and corrosion prevention.
Regular absorption chiller maintenance costs less than major repairs, such as emergency absorption chiller leak repair or full system replacement. The Air-Conditioning, Heating, and Refrigeration Institute shows that a well-maintained chiller operates with a lower life cycle cost. If you’re searching for chiller repair near you, our nationwide team supports urgent and scheduled repairs for all systems.
Key maintenance tips:
Maintain the Purge system: The purge unit maintains the vacuum in the chiller shell by removing non-condensable gases. Operate the purge pump at least weekly, even if the system is idle, to ensure optimal performance.
Regular Leak-Test: Air leaks reduce system performance and reliability, as absorption chillers require vacuum conditions. Perform pressure tests for advanced leak detection, included in our absorption chiller service checks. Address frequent purging promptly with absorption chiller leak repair.
Test for Tube Leaks: If refrigerant levels rise in the evaporator and LiBr concentration drops, it may indicate a leak in the generator, evaporator, condenser, or absorber tube. Immediate nitrogen pressure testing is needed to identify and replace or plug faulty tubes.
Check for Tube Fouling or Scaling: If capacity drops, clean the tubes. Cleaning frequency depends on water quality, atmospheric contamination, and operating conditions. For open cooling tower systems, condenser tubes should be cleaned annually. Our services include scheduled descaling and chiller de-crystallisation tailored to your water conditions.
Our industrial chiller maintenance services include scheduled descaling based on your water conditions.Maintain the Pumps: Absorption chillers use hermetically sealed canned motor pumps. Regularly check pump bearings for wear and clean the internal strainer to ensure proper cooling.
Ensure Proper Conditioning of LIBR: Maintain sufficient inhibitor and alkalinity levels to prevent internal corrosion of the shell and tubes. Annual LiBr sampling is essential for maximum protection.
Have you checked your purge system this week? If not, you could be compromising your entire cooling system without even realising it.
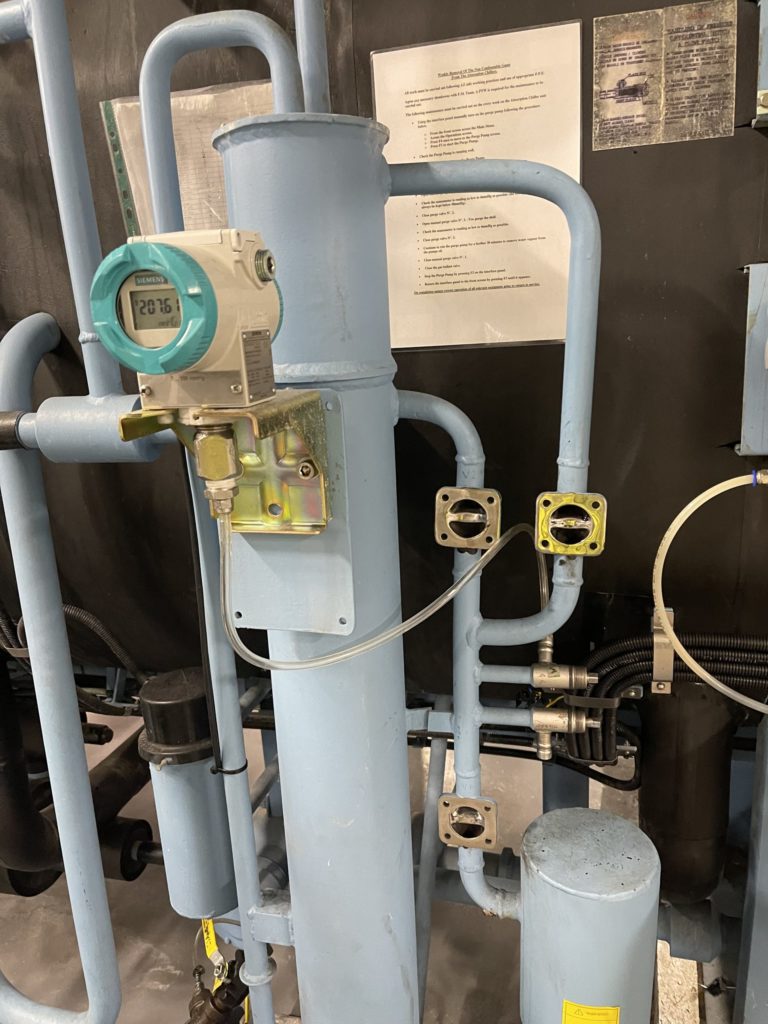

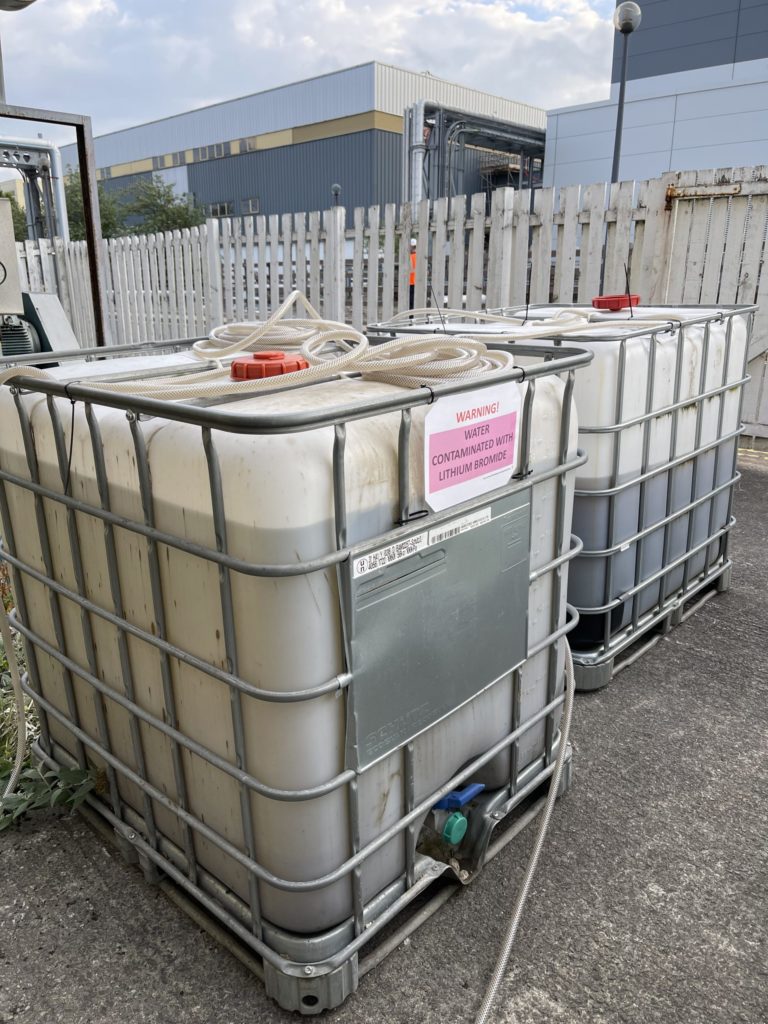
Common maintenance mistakes to avoid…
- Not Having Regular Inspections: Routine inspections are critical for identifying early signs of wear, leaks, or blockages that affect absorption chiller efficiency.
- Insufficient Cleaning of Heat Exchangers: Fouling and scaling on heat exchangers hinder heat transfer, critical for cooling. Regular cleaning prevents performance loss.
- Ignoring Solution Concentration and Quality: Changes in LiBr concentration impact heat transfer and performance. Regular lithium bromide analysis ensures optimal operation.
- Neglecting the Purge Unit: Non-condensable gases (NCGs) reduce efficiency if not removed. Regular purge unit maintenance is essential for vapour absorption chiller fix.
- Overlooking System Pressure Checks: Precise pressure maintenance in the generator, evaporator, absorber, and condenser is crucial. Neglecting checks can lead to inefficient operation or component damage.
- Improper Water Treatment: Poor water treatment causes scaling, corrosion, or biological growth, reducing efficiency and lifespan. Our hot water chiller service includes proper water treatment protocols.
- Ignoring Manufacturer Guidelines: Failing to follow recommended procedures for cleaning, servicing, or replacing components can lead to improper repairs or neglect.